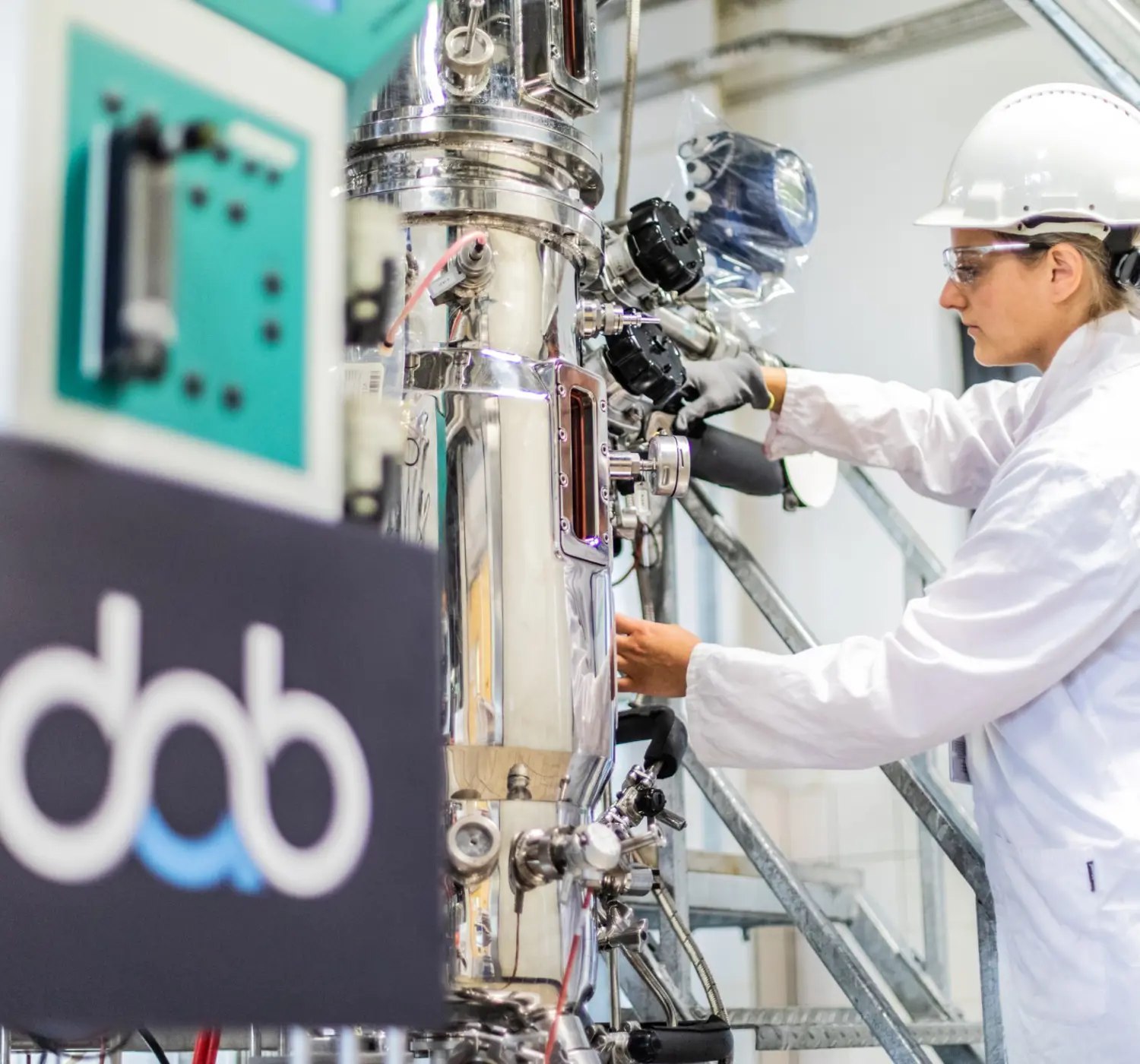
For the production of vitamins, paints or fragrances, we often use fossil raw materials, such as oil. This can be done differently. In Delft, several companies are working on production based on renewable raw materials, such as sugar and wood waste. This is relatively expensive. Start-up company DAB has developed a technology for faster and cheaper ‘green’ production.
For centuries, bacteria, yeasts and fungi have been making useful products, such as beer and cheese, through fermentation. By modifying those bacteria and yeasts, they can also make other products. Such as, for example, vitamins, fragrances or chemical building blocks. They do not use fossil, but renewable raw materials, such as sugar beet residues. This production method greatly reduces CO2 emissions. Unfortunately, it is relatively expensive.
More product, less investment
DAB has found a way to speed up these ‘green’ fermentation processes and make them cheaper. CEO Eric van der Meer: “Fermentation is often done in large tanks with water, bacteria or yeasts, and growth medium. The process yields a fairly small amount of product, hidden in a huge amount of water with waste. We are now coming up with a patented technology developed at Delft University of Technology. This technology allows us to periodically remove the product from the fermenter, making the microorganisms work more efficiently and produce more. Also, we need to clean up much less water to extract the product, and we can get by with smaller tanks.” The technology is suited for a wide variety of products, from inexpensive bulk goods to expensive fragrances and dyes or chemical building blocks.
Demonstration scale
The technology makes production with biobased feedstocks considerably cheaper – exactly what is needed to compete with fossil-based production. “We can make green fermentation commercially attractive,” says Van der Meer. But DAB is still a young company. “Our technology has now proven itself on a pilot scale at the Bioprocess Pilot Facility on the Biotech Campus Delft. We now want to demonstrate that it also works on a larger scale.” In this stage, it is necessary to invest heavily in demonstration units according to industrial standards, without much income in return. “Fortunately, we are in the right place, have the support of solid investors and the ‘Delft University of Technology quality label’,” says Van der Meer. By the end of 2021, the proof should be largely in place, after which the technology can enter the market in 2022. “I’m hugely optimistic about it!”, concludes Van der Meer.
Want to learn more about DAB? Check out their community page